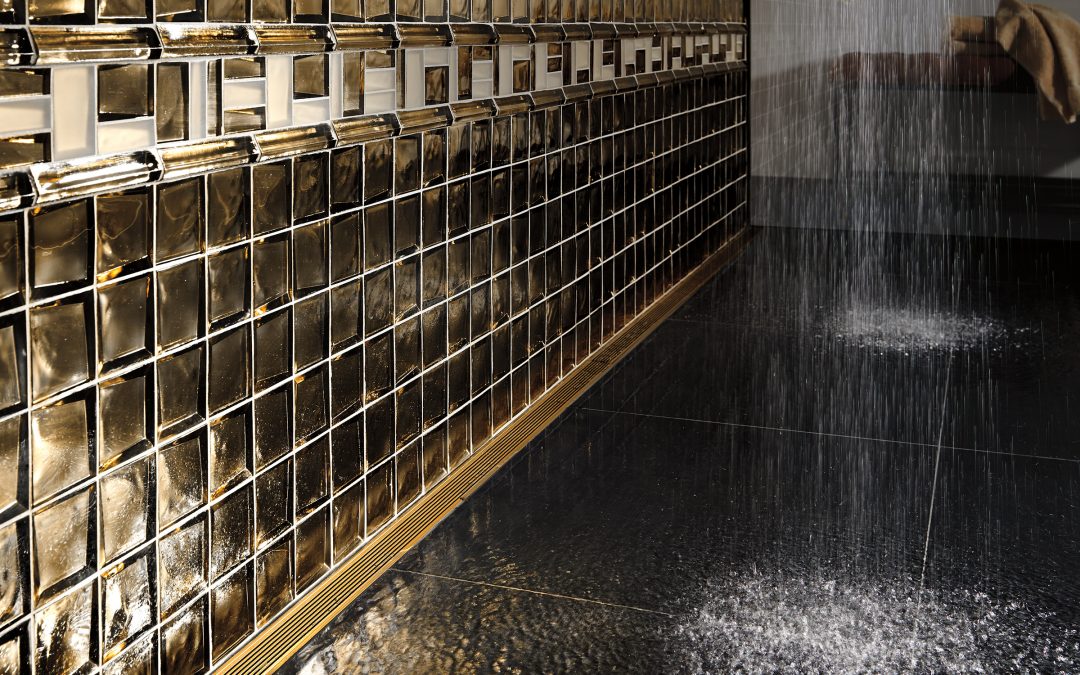
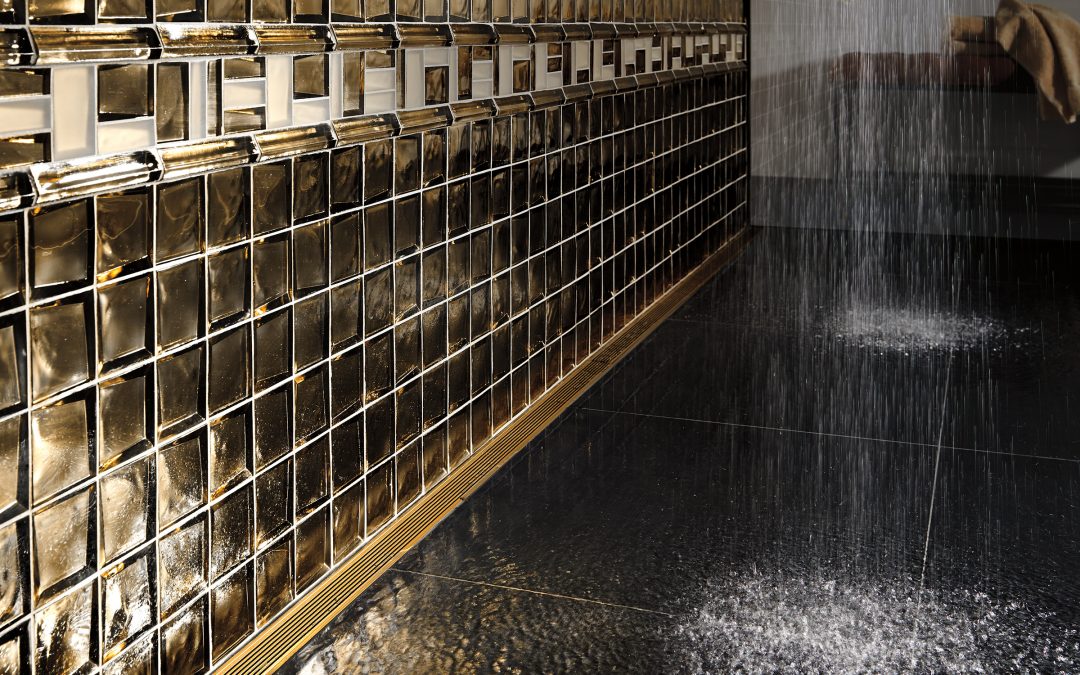
by Rakesh Ramkarran | Jul 21, 2021 | Designer Trends
Sanctuary, safe-haven, retreat. Bathrooms have come a long way since its origin as a space for a quick bodily refresh. What was once a communal place not even part of a home, has now become one of the most private and sacred focal points of residential design. Join us...
KBIS - Booth# N1763
February 25-27, 2025
US residential installations use a 2ā waste line, which has an average capacity of 9 GPM at ½ā head of water, assuming proper venting.
There are many variables that influence flow rates and how drains perform. Our listed GPM (gallons per minute) on Infinity DrainĀ® products are based on having a āhead of waterā that is traveling at ½ā high. Different head heights will change flow rate. Without calculating a specific install, use our flow rate as a general guideline. The following variables should be considered when choosing and locating a linear drain.
Variables to consider:
The answers to the above questions fall into the equation of determining the proper type of drain, outlets necessary, and location of the drain. These variables can vary drastically from installation to installation, and because of this, it is difficult to have an absolute flow rate.
Adding additional 2ā outlets and tying them to a 3ā waste line will significantly increase the flow rate.
High Flow drains are designed to be connected to a 3″ waste line (not standard) and will have an average capacity of 21 GPM.
There are many variables that influence flow rates and how drains perform. Our listed GPM (gallons per minute) on Infinity DrainĀ® products are based on having a āhead of waterā that is traveling at ½ā high. Different head heights will change flow rate. Without calculating a specific install, use our flow rate as a general guideline. The following variables should be considered when choosing and locating a linear drain.
Variables to consider:
The answers to the above questions fall into the equation of determining the proper type of drain, outlets necessary, and location of the drain. These variables can vary drastically from installation to installation, and because of this, it is difficult to have an absolute flow rate.
The Solid grate showcases a fully stainless steel cover. A minimally sized gap surrounds the grate on all sides to provide the necessary drainage to evacuate water efficiently.
Infinity Drain slotted perforated grates are made from 16 gauge, 304L stainless steel.
Infinity Drain Wedge Wire blends contemporary styling with durability. The signature āInfinityā look is created by V-shaped wires that run parallel to each other and are welded together with a spacing of precision. Grate openings widen inwardly to serve as a primary strainer for debris while allowing water to flow freely.
If youāre going for a sleek, minimalist look, choose a drain that has a simple square pattern. It will add a statement to your shower, without taking away from the clean look.
Make the drain disappear. The Tile Insert Frame allows the drain to truly disappear into the shower floor. Flooring material is set into the tray and a minimally sized, yet sufficient, gap provides the necessary drainage to evacuate water efficiently. This grate style provides the illusion of an extension of your shower floor over the drain.
This style is the perfect mix of everything that you are. It can be a combination of the styles you love ā from traditional, simple lines to elegant, dramatic pieces, along with romantic, intricate textiles. Choose a drain that is an artistic balance between modern-day chic and vintage classic.
With solid textiles, black and white features, and pops of gold or brass, you can achieve a timeless feel with your design. Add a hint of glamour with a sophisticated design in a decorative finish to liven up your shower and bring in a familiar pattern.
The vibe of industrial designs has become a wildly popular trend. Cement features, exposed pipe, and glass partitions, create a functional, proletarian feel. Pairing this look with a drain that has a slight decorative edge will add some dimension to your more utilitarian surfaces.
If youāre going for a sleek, minimalist look, choose a drain that has simple straight lines. It will add a statement to your shower, without taking away from the clean look.
This style marries the timelessness of traditional design with the clean lines of contemporary. A clean, criss-cross drain design will add a clean transitional detail to the center of the shower that complements this look seamlessly.
Infinity Drain square perforated grates are made from 18 gauge, 304L stainless steel.
Infinity Drain circle perforated grates are made from 16 gauge, 304L stainless steel.
The Solid grate showcases a 3/16 inch thick, fully stainless steel cover. A minimally sized gap surrounds the grate on all sides to provide the necessary drainage to evacuate water efficiently.
The Slot Linear drain provides a narrow 3/8-inch drainage gap that virtually disappears into its surroundings.
Infinity Drain Offset Slotted perforated grates are made from 16 gauge, 304L stainless steel.
Infinity Drain slotted perforated grates are made from 16 gauge, 304L stainless steel.
Consists of two layers of waterproofing.
The primary waterproofing layer is a traditional type of waterproofing. This shower pan is built to be mechanically fastened to a drain body. The secondary waterproofing layer is a modern type of waterproofing. This waterproofing is above the primary layer and is applied to the primary mortar bed and bonds directly to the flanges of the drain.
The type of waterproofing can help determine which linear drain series to specify. If using a traditional type of waterproofing, the professional will typically build a shower pan with PVC, Vinyl, Lead, Hot Mop, Copper or Fiberglass material. If using a modern type of waterproofing such as liquid or a fabric install, the professional can waterproof over a greater floor area to build a barrier free or zero threshold installation.
Most often, plumbers will install a linear with a clamping floor drain to be used with traditional waterproofing.(Example: Rubber Liner – ChloraloyĀ®)
Most often, tile setters will install a linear with modern type of waterproofing. (Example: SchluterĀ®-KERDI membrane system)
Note: Some areas in the US require specific types of waterproofing. Be sure to check with your installation professional about the waterproofing method being used before selecting a drain.
Deciding between a barrier threshold (curb) or barrier-free (curbless) installation is critical when a linear drain is being considered.
For threshold installs, we recommend the drain run exactly wall-to-wall to block any water from leaving the shower or wet area. We do not recommend linear drains less than 2ā wide or Tile Insert Frame linear drains for threshold installations without a curb due to the lack of channel width needed to sufficiently catch the water.
Installing a shower drain without a curb, barrier, or threshold creates a seamless look with easy accessibility to the wet area. To achieve an ideal installation, floor heights should be equal between the shower area (wet area), outside the shower (dry area), and next room.
Please consult a licensed professional when determining which installation is possible.
Ā Ā
Infinity Drain Wedge Wire blends contemporary styling with durability. Made of 316L marine grade stainless steel, the signature āInfinityā look is created by V-shaped wires that run parallel to each other and are welded together with a spacing of 3mm. Grate openings widen inwardly to serve as a primary strainer for debris while allowing water to flow freely.
Infinity Drain 3mm Wedge Wire is available in 1-1/2″ and 2-1/2″ widths.
Infinity Drain Wedge Wire blends contemporary styling with durability. Made of 316L marine grade stainless steel, the signature āInfinityā look is created by V-shaped wires that run parallel to each other and are welded together with a spacing of 2mm. Grate openings widen inwardly to serve as a primary strainer for debris while allowing water to flow freely.
Infinity Drain 2mm Wedge Wire is available in 1″, 1-1/2″, 2-1/2″, 3-7/8″, and 5″ widths.
The Tile Insert Frame allows the drain to truly disappear into the shower floor. Flooring material is set into the tray and a minimally sized, yet sufficient, gap provides the necessary drainage to evacuate water efficiently. This grate style provides the illusion of an extension of your shower floor over the drain. The Tile Insert Frame is constructed of 12 gauge or 16 gauge, 304L stainless steel.
Also called a trough or trench drain, a linear drain is a rectangular-shaped drain that allows for the use of larger format floor tile and the ability to pitch the floor in one direction. This offers an advantage from the traditional center drain installation, where the floor must slope in four directions in order to drain the water properly.
Benefits of a linear drain installation include:
Ā
Also called a point drain, a center drain is a circular or square-shaped drain that requires the floor to be sloped in four directions in order to drain the water properly.
Deciding between a barrier threshold (curb) or barrier-free (curbless) installation is critical when a linear drain is being considered.
For threshold installs, we recommend the drain run exactly wall-to-wall to block any water from leaving the shower or wet area. We do not recommend linear drains less than 2ā wide or Tile Insert Frame linear drains for threshold installations without a curb due to the lack of channel width needed to sufficiently catch the water.
Installing a shower drain with a curb allows more flexibility in drain choices.
Please consult a licensed professional when determining which installation is possible.
Ā Ā
Heated liquid tar is applied or āmoppedā on the shower area to create the shower pan and is similar to waterproofing a roof with tar. This installation is most common in California. Similar to fiberglass waterproofing.
Infinity Drain FCS Series pre-affixed with SchluterĀ®-KERDI fabric offers seamless installation and a system warranty backed by Infinity Drain and Schluter. This product complies with SchluterĀ®ās shower system warranty program and is backed by both Infinity Drain and Schluter. The new Infinity Drain FCS Series delivers peace of mind performance for designers and installers and is available on all Infinity Drain grate styles, finishes ā including custom linear drains.
Sheet membrane that bonds directly to the drain flange with an adhesive and is sold in most tile suppliers. Corners (in and out) are available to avoid folding. If the shower pan area is larger than the roll dimensions, it must be seamed or joined together. Tile can bond directly to waterproofing.
Roll or paint-on liquid membrane that can be applied on floors, walls, and ceilings and bonds directly to the drain flange. The total install time is shorter than traditional waterproofing methods and typically saves 2 to 3 days. Tile can bond directly to waterproofing.
A plastic sheet available at most plumbing suppliers and sold in rolls of 4′, 5′ and 6′. The membrane is layered between mortar beds and the corners are folded to create the shower pan liner. If the shower pan area is larger than the roll dimension, it must be seamed or joined together. Tile cannot bond directly to this type of waterproofing.
A rubber sheet available at most plumbing suppliers and sold in rolls 4′, 5′ and 6′. The membrane is layered between mortar beds and corners are folded to create the shower pan liner. If the shower pan area is larger than the roll dimension, it must be seamed or joined together. Tile cannot bond directly to waterproofing. CPE Membrane is also branded as Chloraloy⢠by Noble.
A metal sheet that is formed to create the shower pan area. The membrane is layered between mortar beds and the corners are folded to create the shower pan liner. If the shower pan area is larger than the sheet dimension, the lead material must be welded together. This install is more common in metropolitan areas where code may require a metal pan. Tile cannot bond directly waterproofing.